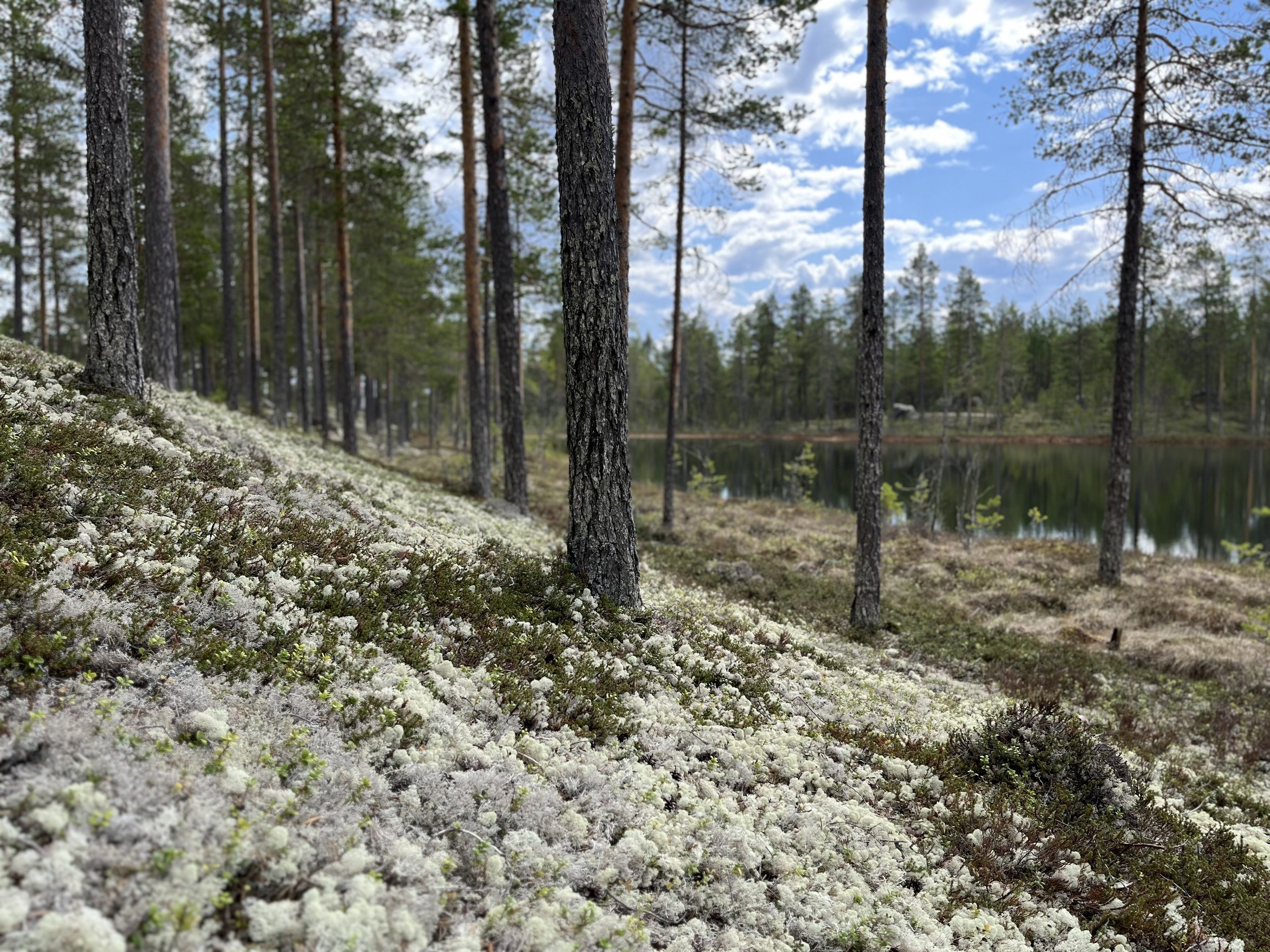
Sustainability
A commitment to transparency
At Nordgröna, we believe that transparency is the cornerstone of genuine sustainability. By being open and honest about our practices and their impacts, we hope to inspire not just better consumer decisions but a broader commitment to responsibility and integrity in the industry.
We use regrowing and recycled materials where possible and we continuously work to innovate more sustainable options.
Materials
Our production facility in Arlöv runs on 100% renewable energy. We minimize the consumption of energy and fossil fuels by optimizing packaging design and palletization. Additionally we reuse materials in product packaging throughout the production chain.
Production
VOC emissions & chemicals
Our products meet high standards for VOC emissions. We prioritize sustainability by minimizing potentially harmful chemicals and selecting materials with a low environmental impact.
We prioritize fossil-free transportation for road freight whenever feasible. Other than that, we offset our carbon footprint through climate compensation.
Transportation
Our work towards a better future
In the coming years, Nordgröna aims to systematically improve the environmental performance through planning, implementation, monitoring, and action. As part of this effort, we will measure and reduce our ecological footprint.
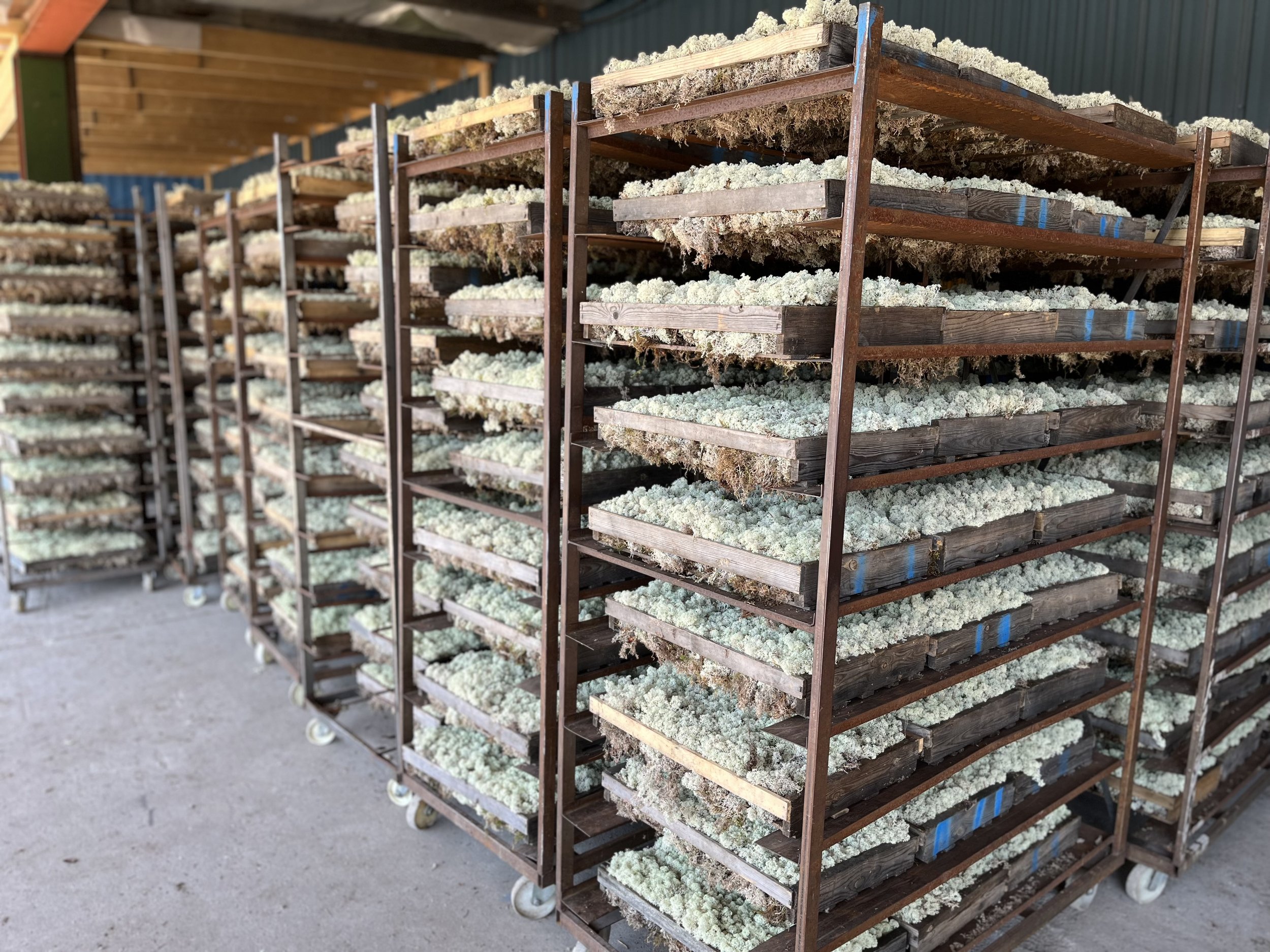
Our regrowing materials
Reindeer Moss
Reindeer moss, or Cladonia stellaris, is a carpet-forming lichen growing freely and abundantly in boreal and arctic regions around the circumpolar north. It is found primarily in areas of alpine tundra and is extremely cold-hardy.
-
A lichen is an alga, which lives in symbiosis with a fungus. The fungus provides support and protection and absorbs water while the algae provides energy and sugar through photosynthesis.
Lichens do not have roots and absorb water and mineral nutrients from the air. This also makes lichen sensitive to pollutants – they only grow where air quality is high.
-
Cladonia stellaris, characterized by relatively fast growth, can be harvested up to 20% of the mat's size every 5 to 6 years without endangering the lichen resource (Roturier et al. 2017)
-
No. Harvesting lichen is an ancient tradition where the material has been used for various purposes, including animal feed, insulation material, and decoration.
-
No and yes. Reindeer do consume lichen, but harvesting is seasonal and typically occurs between April and October when the ground is free of snow. Therefore, we do not harvest lichen during a critical period when reindeer have the greatest need for it. Additionally, lichen is also picked and saved for reindeer so that they have enough food, especially during winter when the deep snow makes it harder for them to reach their food sources.
-
An increasing number of research institutions demonstrate a range of positive health effects for humans—both from being in nature, being close to natural materials, and even from viewing images of nature. Additionally, they contribute to enhanced focus and productivity in the workplace.
-
Our supplier is certified by ISO 9001 & 14001.
-
From forest to function:
The material journey of Nordgröna Reindeer Moss
➔
-
1. Lichen harvested by hand
Our Reindeer Moss is hand-harvested in Härjedalen, Sweden, and the Norwegian region of Rendalen. This Moss (actually lichen), known for its relatively rapid growth, is collected using specific schedules to ensure sustainability. Harvesters rotate and gather limited amounts from diverse locations to protect this valuable resource.
-
2. Drying and transportation
Following harvesting, the lichen is initially dried outdoors and then placed in a drying room for approximately 12 hours. Once the drying process is complete, the lichen is transported in full trucks powered by fossil-free fuel (HVO) to our production facility in Arlöv, in southern Sweden. Our facilities are powered by renewable electricity.
-
3. Dyeing and preservation
In Arlöv, we dye and preserve the lichen using a water-based blend of sea salt, pigments, and additives that we have developed. Following the preservation process, the lichen is dried in a drying room and subsequently becomes ready for use in our products.
-
4. Assembly by hand
Our skilled team assembles all moss products by hand, and when preparing for packaging, we repurpose the original cartons that the lichen came in as protective filler material.
-
5. Shipping the products
The moss products are shipped globally to customers, with all road freight being climate-compensated. Furthermore, we reduce the consumption of fossil fuels linked to transportation by optimizing packaging designs and pallet configurations.
-
6. Once in place
When your moss product arrives, it is completely maintenance-free. It is designed and produced to last a long time and the colouring and preservation process has undergone VOC emission testing (CDPH) which means the moss has been checked to be non-toxic.
-
7. Recycling
The products can be disassembled and sorted according to instructions. However, if you're unable to keep your moss product, we suggest offering it to a dear friend instead of throwing it away. We can almost guarantee that you'll become quite popular.
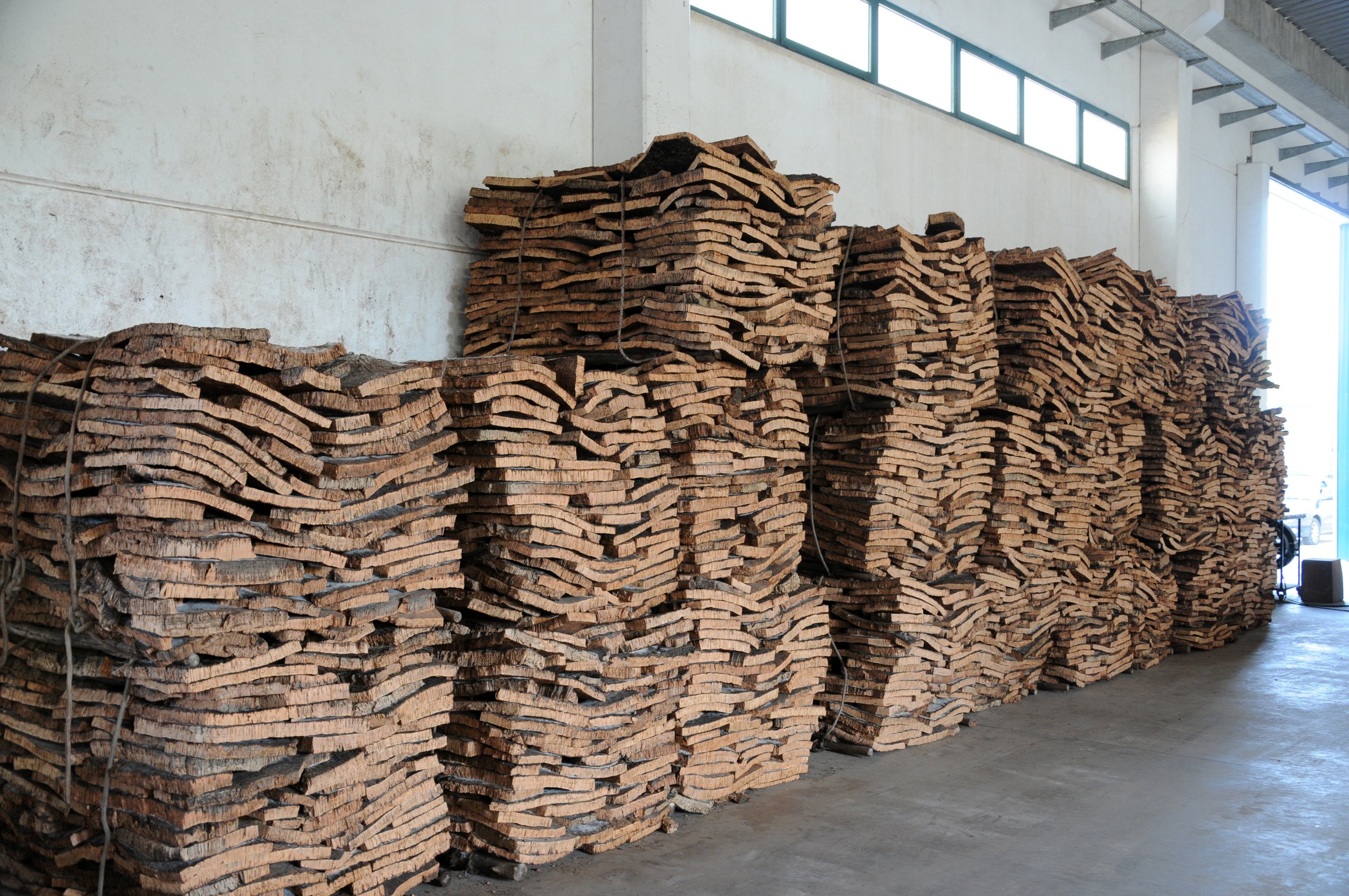
Cork
Cork is the outer bark of the cork oak tree, a natural material used by humanity for over 5000 years.
After the first harvest, the bark is carefully removed from the tree every nine years until the oak tree is about 150 years old. Because cork bark removal requires a high level of expertise, it is one of the best paid agricultural professions in the world.
-
The conservation of cork oak forests plays a crucial role in the world's ecological balance, combating climate change and desertification, and maintaining biodiversity. Due to its biological richness and variety, but also its extreme vulnerability, the cork oak forest is one of the world's 36 biodiversity hotspots, similar to the Amazon and African savannahs.
-
Cork oak forests contribute significantly to air quality and the future of the planet. Over its lifetime, the cork oak becomes a massive store of carbon dioxide and reduces greenhouse gas emissions, the main cause of climate change.
-
Each year, cork oak forests absorb up to 14 million tons of carbon dioxide, and this ability to sequester carbon dioxide is transferred to processed cork products, including Nordgrönas Saga. During the natural regeneration process that follows logging, the tree's ability to absorb carbon dioxide increases up to five times.
-
The manufacturing process also creates a cork dust - a kind of biomass. It is reused and provides over 60% of the energy used in the factory.
-
Our supplier is certified by the Forest Stewardship Council (FSC®) and the Program for the Endorsement of Forest Certification. Raw materials used are FSC® or PEFC certified and come from responsibly managed forests.
-
Turning wasteful into useful:
The material journey of Nordgröna Cork
➔
-
1. Raw material extraction
Our hand-harvested cork, sourced from Portugal, comes from trees uniquely capable of recovering after each harvest of bark. In this traditional practice, skilled artisans carefully remove the outer bark, sparing the inner layer, allowing the tree to rejuvenate. Initially harvested around 20 years of age, two-thirds of the bark is collected during the first harvest.
-
2. Manufacturing
After each harvest, the bark is dried in the sun for six months before being taken to the factory where it is boiled and dried again. Wine corks are punched out of the thick bark, and the residual material from the process becomes cork granules which, together with the binding material polyurethane, are molded into Nordgrönas Saga.
-
3. Packing and transportation
In the manufacturing process, cork dust generates a type of biomass that is ingeniously repurposed, contributing to over 60% of the factory's energy consumption. The factory utilizes efficient palletized packaging before the products are transported to us in Arlöv.
-
4. Shipping the products
The cork products are shipped globally to customers, with all road freight being climate-compensated. Furthermore, we reduce the consumption of fossil fuels linked to transportation by optimizing packaging designs and pallet configurations.
-
5. Once in place
When your cork product is delivered, it's completely maintenance-free, and all our products are designed and manufactured to last a long time.
-
6. Recycling
Agglomerated cork is sorted as residual waste. However, if you no longer have the opportunity to keep your product, we recommend that you give it to a truly good friend.
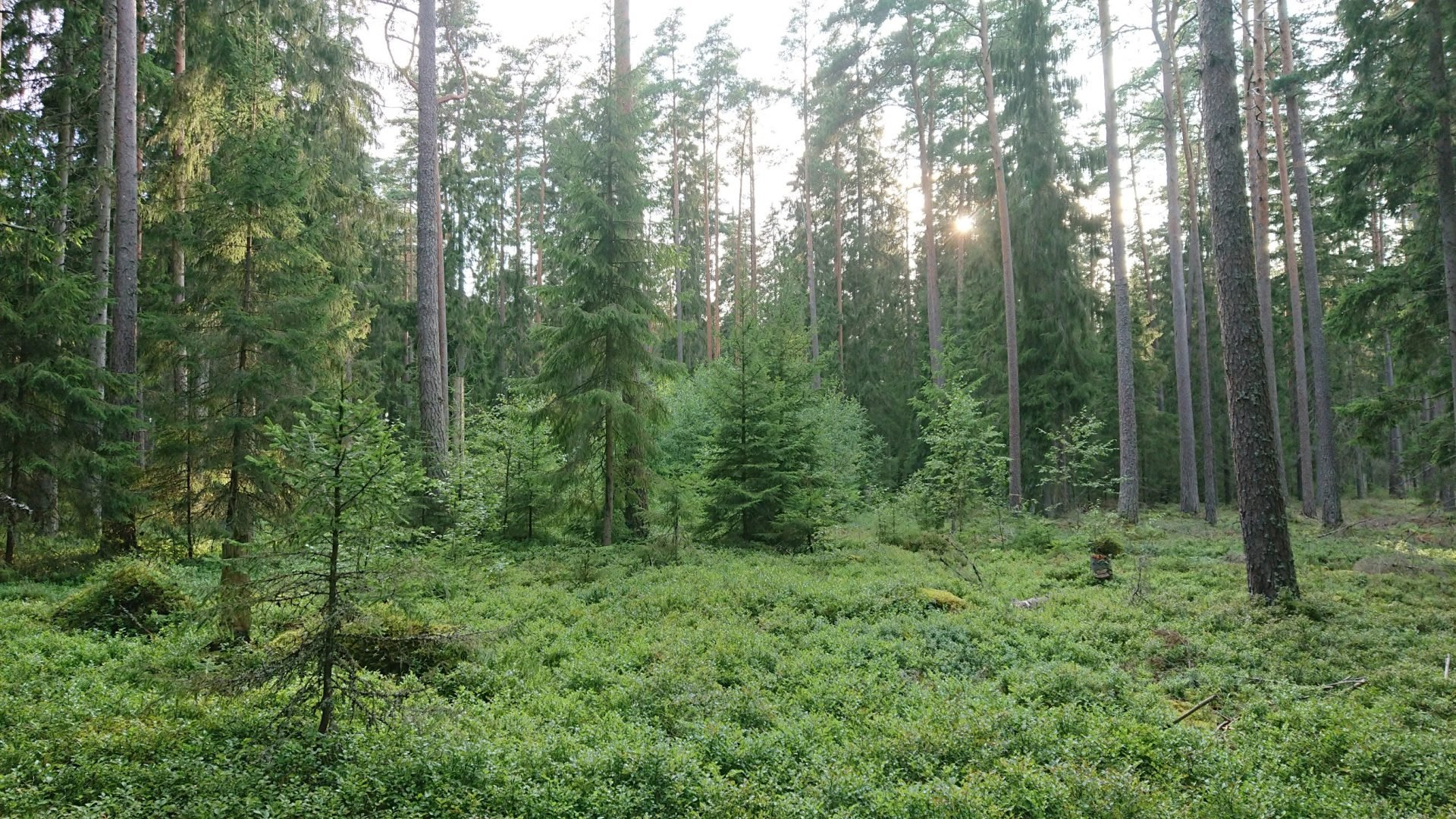
Clearcut-Free Timber
Clearcut-free forestry means not cutting down all the trees at once. Instead, only some trees are removed to keep the forest healthy and full of different trees and living species.
-
The timber is selectively harvested, ensuring that only mature or unhealthy trees are taken, while younger trees are left to continue growing. This careful approach allows the forest to regenerate naturally, preserving its biodiversity so that plants and animals can thrive.
-
Clearcut-Free Timber helps protect forests from destruction, allowing trees to regenerate and preserving wildlife habitats. Unlike todays logging practices, which releases carbon, intact forests store more carbon, helping fight climate change. This method also preserves soil health, prevents erosion, and supports biodiversity, which is crucial for the long-term survival of species and future generations.
-
By ensuring trees are left to grow and regenerate, Clearcut-Free Timber practices help keep carbon stored in forests, reducing the overall impact on the climate.
-
Nordgröna Clearcut-Free Timber preserves the natural colors and unique characteristics of the wood, making each installation one of a kind. By using different types of wood, products have more variety and character. This also fits with biophilic design, which uses natural materials to create spaces that help people feel calm and connected to nature.
-
Our supplier is certified by the Swedish organization Plockhugget, ensuring that all forestry practices follow strict guidelines for environmental care. This certification guarantees that the timber is sourced supporting forest regeneration, protecting biodiversity, and minimizing negative impacts on the ecosystem.
-
Challenging today's forestry practices
The material journey of Nordgröna Clearcut-Free Timber
➔
-
1. Where the forest thrives
The timber used in our products comes from a forest near Aneby, Småland, where Plockhugget certified close-to-nature forestry is practiced. This approach avoids clearcutting, instead nurturing the forest as a living ecosystem. It strengthens biodiversity, stores more carbon, and helps trees better withstand storms, fires, drought, and pests. It also preserves wildlife habitats, recreational areas, and the natural beauty of the landscape.
-
2. Clearcut-free harvesting
Clearcut-free forestry means only some trees are removed, not all at once. Foresters carefully select trees to keep the forest healthy and diverse. The process is planned to reduce damage, protect ecosystems, and preserve important areas. Some mature trees are left for biodiversity, and smaller equipment helps protect the ground.
-
3. The sawmill
After harvesting, the trees are taken to a nearby sawmill, where they are cut and planed. Clearcut-free forests naturally have a mix of tree species, and this variety is reflected in the timber. By choosing different species and lengths, we reduce waste and preserve the wood’s natural look and color. This gives our product its unique beauty and character.
-
4. Final touches
This is where our Flora comes together. After the timber is processed at the sawmill, it is shipped to the Nordgröna facility in Arlöv, Sweden. There, we apply an oil wax finish for durability and, if needed, a fire coating to meet your specific requirements.
-
5. Shipping Flora
Flora is shipped worldwide, with all road freight climate-compensated. To further reduce fossil fuel use, we optimize packaging designs and pallet configurations for efficient transport.
-
6. Once in place
Flora is designed for long-lasting use without regular maintenance. Since it's made from solid wood, any scratches or damage can easily be repaired by sanding and reapplying wax.
-
7. Recycling
Solid wood can often be reused, repurposed, or recycled into new products, depending on local recycling options. However, if you no longer need your Flora, we recommend passing it on to someone who will appreciate it, so it can continue to live on.